Swing Lever Bushing
by George Lyle and Michael Pjetraj
George Lyle writes:
The kits are pretty simple, consisting of two bushings, the hinge pin, and a new bottom cap.
I did my '71 so long ago that I can't recall the source of the parts. It might have been the local FLVWPS. The parts were German, but not in a "VW" marked box.
The one big tip I have is to avoid hammering the bushings out. It's a real pain and there is a very real possibility of damaging something.
You do need a tool to press them in and out. I made one from a few heavy washers, a deep socket (large enough for the bushing to fit inside), and a 1-foot length of 3/8 all-thread. You grind a washer to be slightly smaller than the ID of the bushing. Remove the bottom cap and pivot pin. Place the washer on top of the upper bushing. Thread the all-thread, through the deep socket, up through the beam and through the washer. Secure this with a nut. The lower end of the rod has two nuts jammed together and a single nut that you will use to pull out the bushings. You hold the jammed nut with a wrench, and use another wrench to tighten the loose nut. This pulls the top washer slowly through the beam, pulling the bushings ahead of it.
Works much better than a hammer!
I read a lot about reaming the bushings to fit, but mine didn't need reaming at all. Might be an early bus thing.
The new bottom cap was impossible to press into place. I could have made it fit with a little fileing around the edges, but the old one was still perfect so I put it in instead.
I grease the swing lever and the torsion bars every other oil change. this is probably too often but grease is cheaper than repairs.
Michael Pjetraj writes:
George's method should work pretty well. I personally had a problem with the force that was necessary with using the all thread the way I had it set up.
Another way (sort of the same):
I decided to use a C clamp, a socket whose OD is almost the same as the bushing but just less than the ID of the housing, a piece of flat bar (3" long and 1/4" thick roughly) and a piece of PVC coupling (I think 2.5" in diameter ~ 2" long).
You will need to disconnect the E-brake directly above the center pin. You will also need to move the drag link and relay arm out of the way (bigger pain than it sounds - good time to replace the drag link as well since you may ruin the boots removing the piece) and remove the grease nipple for the center pin. Read the Bentley or Haynes account on clamping the center pin when you loosen it due to a spring washer in the assembly.
Put the C clamp in position w/ the threaded end toward the ground. Place the flat bar on top of the hole for the center pin (The top bushing extends ~ 0.05 inches above the surface of the hole - but you do not need to worry about displacing it downward since you will be removing it anyway) put the stationary end of the C clamp on top of the flat bar. Now, on the bottom side, put the socket in position under the bottom bushing. The bottom bushing is flush w/ the lip so you need to be really careful and not let the socket get skewed. Keep an eye on it while you start to turn the C clamp. The center pin is not perfectly vertical. The top of the pin is leaned slightly to the back of the bus. Keep this in mind when you are lining up the C clamp. You may need to periodically loosen the clamp and re-tighten. keep rotating the clamp until you feel resistance. Now the bottom bushing has contacted the top bushing. Put the PVC coupler in the place of the flat bar, and then put the flat bar on top of the PVC. The cavity created by the PVC coupler allows room for the bushing to push out. At any time you can put another socket into the center pin hole to reduce the length of the C clamp thread that is extended. Once the top bushing pops out, loosen everything and remove it so the bottom bushing can pop out as well.
Clean all the old grease out of the center pin hole and regrease the area - allows the bushings to slide in easier. Grease the outside of the bushings also.
Put the Bottom bushing in first! This bushing goes flush w/ the hole. The top bushing protudes ~0.05" to prevent the relay arm from scraping the beam (so says Bentley). You want to put the bottom in first so that you can use the surface to push in the top bushing.
Place the C clamp in position w/ the flat bar across the top of the hole and the bottom bushing lined up w/ a thin piece of wood between the bushing and the C clamp. Exert a little pressure, watch the bushing, then slacken the clamp. Check for correct bushing alignment. Then re-exert some pressure. Remember, the pin isn't perfectly vertical, so the bushings won't be either. Once you get the bushing going, it will slide right into position. Put the bar on the bottom and the bushing on top and repeat. Get a feeler gauge for 0.045 to 0.05 and do not allow the bushing to go lower than that.
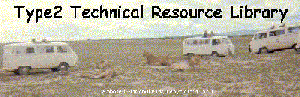
